Shopping Cart [more]
Index of Products
Information
- 900 Series Chemical Process Control Case Studies
- Automatic Rinse Tank Controls
- Boilers and Cooling Towers
- Circuit Board Cleanliness Testing
- Deionized Water
- Environmental Applications
- Fountain Solutions
- Frequently Asked Questions
- Glossary of Terms
- Hemodialysis
- Horticulture
- Hydroponics
- Material Safety Data Sheets
- Operation Manuals / Instructions
- Oxidation Reduction Potential/Redox
- Pool and Spa
- Product Data Sheets
- Reverse Osmosis
- Textiles
Circuit Board Cleanliness Testing
Contamination of circuit boards can bring about severe degradation of insulation resistance and dielectric strength. Cleanliness of completed circuit boards is, therefore, of vital interest.
For those companies who have established circuit board cleaning procedures, the MIL Spec P-28809 has been used as a guideline for control. Now a simple “on line” test for the relative measurement of ionic contamination has been developed.
This fast and economical method for testing circuit board cleanliness uses a Myron L® Company Ultrameter™ 4PII, 6PIIFCE, or 9PTKB, a suitable container, and a mixture of DI (deionized) water and alcohol. The procedure is as follows:
- Mix a stock quantity of solution using 25 parts by volume of Dl water and 75 parts by volume of 99% isopropyl alcohol. The conductivity, measured with the Ultrameter 4PII, 6PIIFCE, or 9PTK should be a maximum of 0.166 micromhos/microsiemens/cm.
- Measure out an amount of the water/alcohol mixture equal to 100 ml per 10 square inches of circuit board surface to be tested (considering both sides of the board but not components), and add 60 ml additional. In other words: 2(L X W) (10ml) + 60 ml = total solution needed.
- Fill a poly “zip-lock” bag or other suitable plastic or glass container with the measured water alcohol solution.
- Using the measured water/alcohol solution in the poly bag, rinse out the Ultrameter's cell cup three (3) times, discarding the rinse solution each time. Fill the instrument cell cup a fourth time and take a meter reading. This value should be 0.166 micromhos/microsiemens/cm or less and is the very clean control (or “comparison”) reading for the test.
- Being very careful not to contaminate the PCB, totally immerse the circuit board in the solution Seal bag. Allow it to soak for three (3) minutes with mild agitation.
- At the conclusion of the soaking, pour the solution directly into the instruments cell cup four (4) times; take the fourth reading.
- Compare the control reading in Step 4 with the reading taken in Step 6. The higher the difference between the two readings, the greater the ionic contamination. Record this final extract reading for comparison with other boards tested in the same manner.
The level of cleanliness needed or desired can only be determined by each individual company. Mil Spec P-28809 can be used as a guideline, or standards can be established based upon available data. In either event, the comparative method using the Myron L® Company's Ultrameter will assist in the determination of that level of cleanliness.
Myron L® Company manufactures a variety of in-line instruments, including resistivity monitor/controllers which are designed specifically for Dl water.
The 900 Series Multi-Parameter Monitor/Controller™ models simultaneously monitor and/or control multiple inputs and outputs. They are autoranging with 3 automatic temperature compensation standards for greatest accuracy (KCl, NaCl, and 442 Natural Water™). Input parameters include resistivity, conductivity, TDS, salinity, pH, ORP, flow/pulse and temperature. The Percent Rejection function of the 900 Series is designed to help quantify the effectiveness of water filtration systems. This is accomplished by comparing the feed water to the permeate (product) water to determine the percent of dissolved solids removed or rejected by the filtration system. The RS-485 serial output allows you to download data to a supervisory computer, PLC or SCADA system.
See table below for additional applications for Myron L® Company instruments and controls.
Other products and companies referred to herein are trademarks or registered trademarks of their respective companies.
**Prices, images and specifications subject to change without notice.**
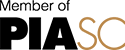

For your convenience, we accept these credit cards:
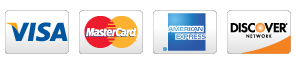